Tips for Streamlining Manufacturing Operations
Efficient manufacturing is vital for the success and sustainability of any industrial enterprise. In today’s competitive landscape, manufacturers must streamline operations to enhance productivity, reduce costs, and improve quality. Implementing key strategies can lead to significant performance improvements and long-term benefits. Whether you are looking to refine your current practices or overhaul your operation system, there are proven methods that can help. Below, we explore essential steps toward achieving a leaner, more effective manufacturing process.
Implementing Lean Manufacturing Principles
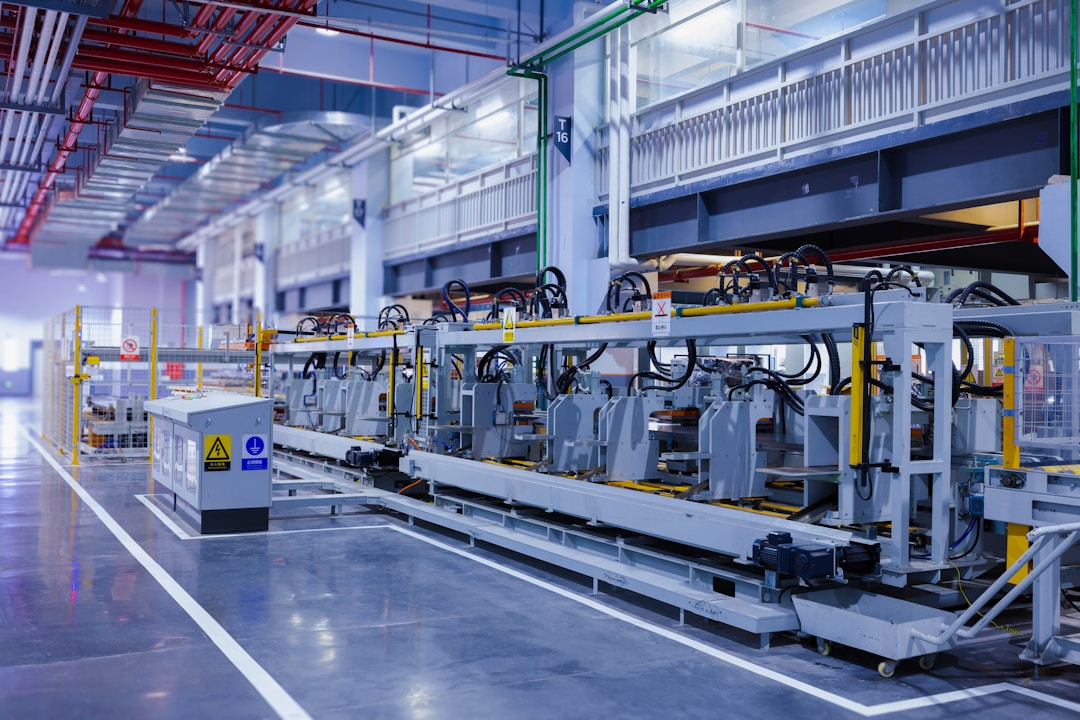
Lean manufacturing principles focus on creating more customer value while using fewer resources and minimizing waste. The lean philosophy is centered on eliminating any activity that does not add value to the end product. By adopting lean practices, manufacturers can improve their operation’s efficiency and flexibility, increasing competitiveness and profitability.
One way to support these improvements is using ERP solutions (Enterprise Resource Planning systems). ERP solutions integrate and automate core business processes, centralizing data and enabling real-time decision-making. This can help manufacturers streamline production, inventory management, and supply chain coordination, ensuring alignment with lean goals and increasing overall operational efficiency.
A core aspect of lean manufacturing is establishing a value stream map, which plots out each step of the production process and highlights where non-value-adding tasks occur. This visualization helps teams understand the current state of their processes and where they can implement changes. Cutting out excess steps and focusing on value-adding tasks allows for a smoother flow of operations and reduces overhead costs.
Another lean principle is the concept of “just-in-time” (JIT) production, which aims to reduce inventory costs and increase efficiency by producing only what is needed when it is required. This system relies heavily on accurate demand forecasting and quick, flexible response to market changes. However, it requires a high level of coordination and communication within the supply chain to be effective.
Embracing Automation for Enhanced Production
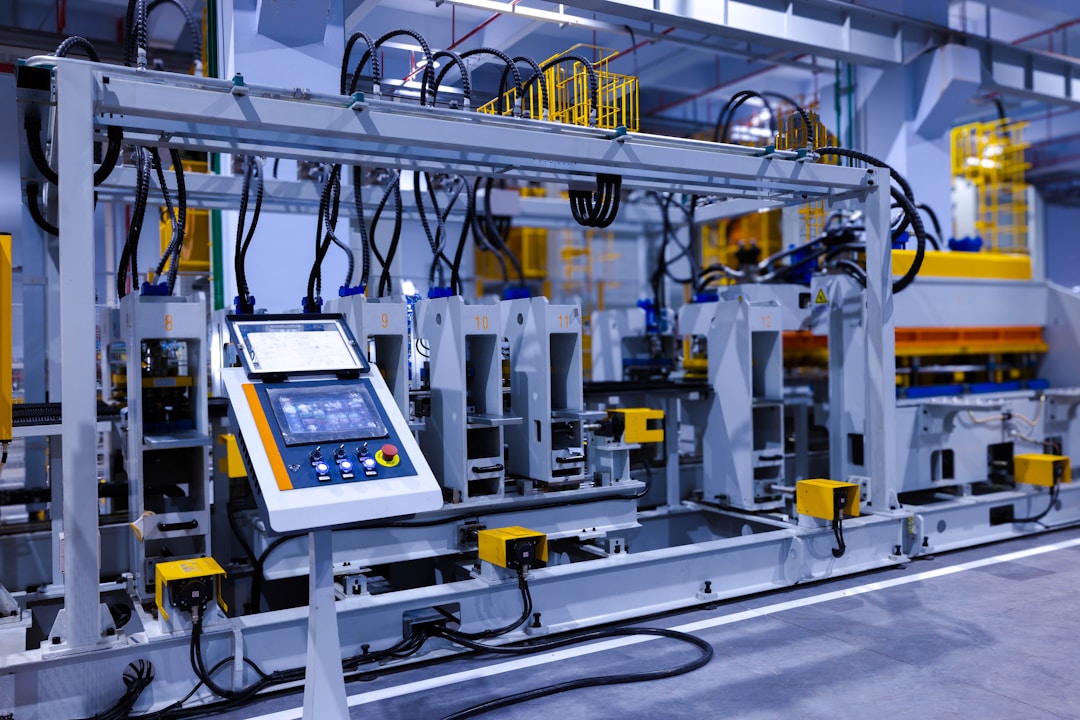
Automation integration into manufacturing operations can vastly improve production capacity and consistency. Automated systems can handle repetitive tasks with greater precision and speed than human labor, freeing employees to focus on more complex and strategic aspects of the manufacturing process. Investing in automation can also improve safety conditions, reducing the risk of accidents on the manufacturing floor.
Incorporating robotics into assembly lines or using automated guided vehicles (AGVs) for material handling are common forms of automation in modern manufacturing facilities. These technologies increase throughput and ensure the consistent quality of products, as they remove the variability associated with human operation. Automation can be customized to fit specific manufacturing needs and scaled as an operation grows.
While the initial investment in automation can be significant, the long-term benefits often outweigh the costs. Automated systems typically have a high return on investment due to the savings in labor, reduced production times, lower error rates, and decreased waste. Staying competitive in the market often necessitates embracing these technologies to meet the demands of high production volumes and precision manufacturing.
Moreover, automation does not solely apply to physical tasks; software automation is equally essential. Artificial intelligence and machine learning advancements enable innovative ERP systems and other software tools to streamline data analysis, quality control, and predictive maintenance. This kind of digital automation can significantly accelerate decision-making and enhance operational resilience.
Integrating Supply Chain Management with Operations
Integrating supply chain management with manufacturing operations is pivotal for achieving seamless production flows. A well-managed supply chain ensures that raw materials and components are available when needed, reducing inventory costs and waste. Collaboration with suppliers and effective communication channels are key to aligning supply chain activities with production schedules.
Advanced planning and scheduling (APS) systems can provide valuable assistance in harmonizing supply chain management with manufacturing operations. Such systems allow for real-time changes to production schedules based on fluctuating supply conditions and customer demand. This level of agility within the supply chain can significantly enhance a manufacturer’s ability to respond to market dynamics and prevent stockouts or overproduction.
Vendor-managed inventory (VMI) is another strategy that can benefit manufacturing operations. Suppliers manage the inventory levels at the manufacturer’s facility in this model. This can improve supplier-manufacturer relationships, as both sides work closely to optimize stock levels and ensure uninterrupted production.
Altogether, streamlining manufacturing operations through lean principles, automation, and integrated supply chain management can significantly improve efficiency, cost savings, and product quality. By embracing these strategies, manufacturers can remain competitive and ensure long-term success in an evolving market.